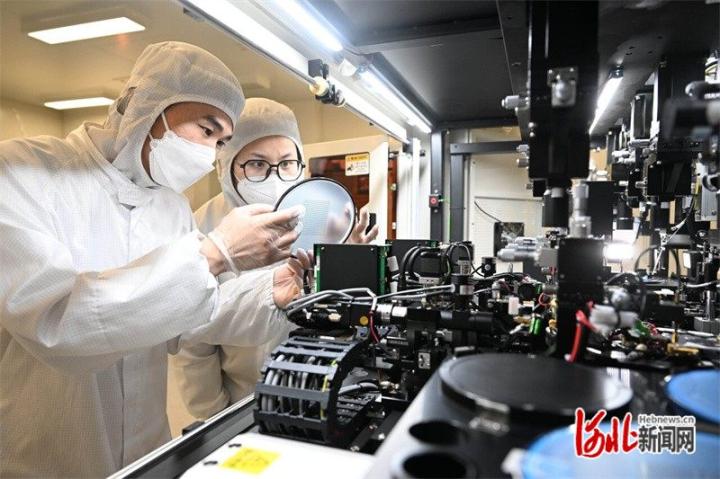
近日,位于石家莊市鹿泉區的河北圣昊光電科技有限公司的技術人員在芯片測試機生產車間查看設備運行狀態。 河北日報記者 張昊 攝
一家生產芯片檢測設備的年輕企業,通過制定標準助力完善國內芯片檢測產業鏈條。
一家全球鋁車輪行業“燈塔工廠”,追求更高品質,用智能裝備代替主觀判斷和人工經驗。
一家建筑防水材料行業領軍企業,把先進質量管理模式融入生產經營各環節,確保了產品質量。
河北省委經濟工作會議要求,聚焦建設標準引領、品質卓越的質量強省,實施質量提升行動,積極構建新型標準體系、產品認證體系、質量追溯體系、監管執法體系,全面加強河北品牌建設和質量管理,在全社會營造精益求精、以質取勝的濃厚氛圍。
企業是質量供給的“細胞”,是質量強省建設的主力軍。近日,記者走進一線,感受企業在質量提升方面進行的探索和實踐。
自產芯片測試機,緣何能替代高價進口設備?
位于石家莊市鹿泉區的河北圣昊光電科技有限公司。芯片檢測車間旁邊的庫房里,一臺芯片測試機“躺”在房間一角,機器表面已經有了灰塵。
“這臺機器,是我們花了400多萬元從國外進口的,但只使用了兩年左右時間。”公司董事長楊勇峰說。
高價的進口設備閑置不用,原因是圣昊公司自己生產出了性能更優、價格更低的替代設備。
圣昊公司是一家芯片后道加工服務型生產企業。最初,公司主要業務是對芯片電性能、光功能等指數進行檢測與評估,判定芯片是否達到設計性能要求。現在,他們的主業又增加了一項:生產芯片檢測設備。
2017年,剛剛成立的圣昊公司從日本訂購了一臺芯片測試機。供貨期8個月、安裝調試3個月,設備正式投用歷時將近一年。設備后續檢修和升級等服務,還需要日本工程師來進行,需要的時間長、費用高。
嘗夠“卡脖子”滋味的楊勇峰決心自己生產芯片檢測設備。引進專家組建研發團隊,經過艱難技術攻關,圣昊公司終于在2020年1月生產出第一臺工業原型機并于當年實現量產。
“我們的產品雖好,但如果沒有標準助力,公司發展還會遇到很大困難。”楊勇峰感慨道。圣昊公司生產的芯片測試機具有測試速度快、價格低、交貨期短、售后服務及時等優點,但最初國內使用廠家并不買賬。一些客戶表示,該類型的芯片測試機在國內沒有同類產品,沒有國家標準、行業標準,他們對產品性能信心不足。
在省市市場監管部門幫助下,圣昊公司參與制定了河北省地方標準《光通信用FP、DFB半導體激光器芯片直流性能測試規范》,并發布企業標準《芯片測試機質量標準》。根據相關標準,芯片測試機各項參數能夠溯源,贏得了客戶信賴。
2020年,圣昊公司生產出50多臺芯片測試機,當年就賣出40多臺,而從日本進口的設備也由于性能不能滿足最新檢測需求而停用。
在圣昊公司芯片人工檢測工序,透過40萬倍電子顯微鏡,記者看到,經過機器檢測的芯片,集成電路清晰完整。“通過檢測,把不合格產品去除,芯片封裝良品率會大大提升。”楊勇峰介紹,通過努力,圣昊公司在一定程度上推動完善了國內芯片檢測的產業鏈條。芯片檢測設備關鍵零件加工精度和設計精度得到提高,芯片封裝前檢測更加普遍。
“標準來源于創新,又是科技成果轉化應用的橋梁和紐帶。”楊勇峰說,公司參與制定的行業標準《光纖通信用半導體激光器芯片測試方法 第1部分:基本光電特性》已于去年12月提交有關部門。標準發布后,將有效推進光電標準與技術同步發展。
“刀補能手”的看家本領,為何讓位于智能裝備?
郎有林是中信戴卡股份有限公司鋁車輪六號工廠機加制造部的工段長。已有18年從業經歷的郎有林,被工友們稱為“刀補能手”,可現在他的看家本領卻在操作環節失去了用場。
刀補,即刀具車削補償。汽車輪轂對尺寸的要求非常高,在實際生產中,因為刀具磨損、模具差異等因素,每次上機后產品尺寸往往不能實現首件即合格,輪轂需要在尺寸檢測后對機床刀補調整。
2月15日,六號工廠流水線上,一只只經過刀補的輪轂有序進入下一個工序。依靠于2021年投用的機加智能質量閉環系統,刀補工序實現一次性調整100%合格,生產效率大幅提升。
“傳統檢測,需要人工不斷調整加工刀具以保障產品精度,最重要的是操作人員的經驗。”郎有林說,刀補數據是成尺寸鏈的,一個數據變化了,其他數據隨之變化。一個成熟的操作人員,刀補工序調機等待時間也要一個多小時。成為成熟的刀補操作工并非易事,不僅要腦子活,還需要數年的實踐經驗。
機加智能質量閉環系統,利用AI算法自動生成刀補值調整方案,實際下發方案加入大數據模型優化機制,可實現算法自學習自優化。“智能裝備代替人工,產品質量明顯提高。”郎有林介紹,系統應用后,機加設備效率大幅提升,調機等待時間下降了42.9%,機加缺陷率降低62.1%。
2021年,中信戴卡鋁車輪六號工廠成為全球鋁車輪行業首家、河北省首家“燈塔工廠”。六號工廠副經理劉興華說,獲評“燈塔工廠”,靠的是獨具行業特色的智能裝備研發和生產工序集成能力,刀補工序的機加智能質量閉環系統正是智能裝備的典型應用之一。
汽車輪轂生產工藝復雜,部分核心環節依賴主觀判斷和人工經驗。中信戴卡把產品質量視為企業的生命線,在人工智能、大數據和5G應用方面進行深入探索和應用,逐步實現了產品質量、產量和成本的可預控。現在的六號工廠,全線工序使用智能調整系統代替了人工維護;通過AI視覺檢測、X光無損探傷人工智能識別系統,為產品配備24小時的“智能醫生”,產品不良率不斷降低。
應用智能裝備提升產品質量,中信戴卡不斷探索。在中信戴卡試驗中心,試驗工程師陳德勝正在操作車輪及懸架道路模擬試驗系統。
“這套系統,把汽車車輪路試從試車場轉移到了試驗室,更接近實際使用場景。”談起這套設備,陳德勝滿是自豪。他告訴記者,歷經3年研發,車輪及懸架系統道路模擬試驗系統于去年11月正式驗收上線,這一試驗系統不僅填補了我國車輪集成懸架系統可靠性測試裝備的空白,更超越了歐美同類技術,達到了國際領先水平,并將幫助中信戴卡建立汽車底盤模塊化產品研發能力,助力企業向模塊化供應商轉型。
首席質量官,如何挑起質量強企大梁?
每隔一小時,質檢部質檢工程師李嬌嬌就要到防水卷材生產第一車間進行生產線產品取樣。
每隔一小時,防水卷材生產車間配料組長趙學磊就要打開配料罐,取出中間物料樣品,然后送到檢測室檢測。
2月28日,來到唐山東方雨虹防水技術有限責任公司,跟隨公司首席質量官、總經理陸殿富體驗全面質量管理如何保障產品質量,記者對這兩個“一小時”印象深刻。
在我國,建筑防水材料用量非常大,生產企業數以千計。陸殿富說,東方雨虹能夠成為這一行業的龍頭企業,原因在于產品質量過硬。“比如普通的防水卷材,生產技術大家都能掌握,比拼的就是質量管理。”
在防水卷材生產第一車間,見到李嬌嬌,打包崗位工人很快把卷氈機從自動模式調整為手動模式,從生產線上取下防水卷材交給她。對防水卷材的幅寬和長度進行現場檢測后,李嬌嬌把卷材樣品帶回卷材力學檢測室,用專業儀器檢測卷材厚度、縱向橫向延伸率和拉力等指標。
根據國家標準,防水卷材需要每1萬平方米進行相關指標的檢測,第一車間每小時產量約為3000平方米,每小時檢測一次,檢測頻率遠高于國家標準。按照生產進度,每更換一批次中間物料都要取樣檢測,則是東方雨虹對生產材料質量嚴格把控的具體體現。
作為首席質量官,陸殿富是產品質量的第一負責人,其職責是確保企業各部門全面實施東方雨虹質量管理體系,把先進的質量管理模式融入生產經營各環節,實現產品質量全生命周期管理。
陸殿富介紹,東方雨虹構建了研發、生產、檢測三個環節互相配合與監督的質量管理體系,使整個質量管理體系具備自我修復和糾正功能,防止產品質量出現波動。從原材料進場到成品出廠,實施五級質量檢測——原材料入廠檢驗、小試驗證、中控檢驗、生產線成品檢驗、庫房成品檢驗,建立和完善過程質量控制體系,近三年產品檢驗一次合格率逐年提升,生產過程廢次品率逐年下降。
首席質量官是企業對質量安全和質量發展全面負責的高層管理人員。2022年9月,省政府印發《關于全面提升產品質量的若干措施》提出,到2023年底,推動全省規模以上工業企業全部設立首席質量官。陸殿富說,東方雨虹于2018年就嘗試實施的首席質量官制度,通過推行先進的質量管理體系和模式,引導企業堅持質量第一,實現質量強企,大大增強了企業競爭力。(河北日報記者 馬彥銘)